Introduction
First, familiarize yourself with the design and capabilities of your chilled-water system. Do the pumps have variable-speed drives (VSDs), and if so, are they programmed to take full advantage of the variable-speed capability?
Situations where VSDs might be used include:
- One pump feeds multiple chillers. The pump flow is "stepped" to match the chillers that are online.
- Cooling loads are linked to outside-air temperature (OSAT), so that the hotter it gets, the more cooling is required, and system flow is increased. Keep in mind, however, that when process-cooling loads are present, they may determine the cooling load independent of OSAT.
There are many ways to configure the system control to use variable-speed pumping, for example:
- Two-way modulating control valves are commonly used. As the control valves for the cooling coil of the air-handling unit (AHU) start to close as the cooling load lessens, the VSD slows the pump to maintain a preset differential pressure in the supply and return piping.
- All valve positions are monitored and the pump speed changes to keep the AHU that requires the most cooling between about 90% and 95% open.
- A modulating bypass allows for minimum flow conditions. A variant of this is to install 3-way valves on the longest hydraulic runs. The flows through these valves would equal the stable minimum system flow rate.
Make sure you understand the control strategy for your own system and how it is configured before starting to diagnose problems.
How This Wastes Energy
Keeping the chilled-water pump at an elevated speed requires more power for the pump motor than would be required if the system responded properly to reduced loads.
Possible Causes of This Symptom
The table below shows some of the possible causes of this symptom. The cause of a symptom can be an energy-performance problem that can be fixed, or it may be explained by an unavoidable aspect of your current system that would probably require a capital project to change. Follow the steps described after the table to determine the possible cause of this symptom. If you find a problem, perform the suggested trend logging to confirm that the problem exists and, later, that you have solved the problem.
Inspection Steps:
- Explanation: Pump is undersized for the connected load.
- Problem: Chiller is not cooling the supply water to the setpoint.
- Problem: Pressure sensor is malfunctioning or improperly located
- Problem: Coil control valves do not follow coil loading.
- Problem: The piping system has a short circuit.
- Problem: VSD control is either in manual mode, overridden, or in bypass mode.
- Problem: System strainers are clogged.
How to Find the Problem(s) by Inspection
Inspection Step 1
Inspect the design drawings for recent modifications to the chilled-water system. Some things to look for:
- Sometimes additions to the system, especially process loads, are made without increasing the pump capacity. When possible, the chilled-water system should be rebalanced after additions to the system. If you find that the pump cannot meet maximum demand, you may need to replace the impeller or the entire pump.
- The pump impeller may have been trimmed in the past when less flow was needed.
Inspection Step 2
Check the chilled-water supply temperature (CHWST). It should be at setpoint, and the differential temperature between CHWST and chilled-water return temperature (CHWRT) should be close to the design condition. If the CHWST is above the setpoint, the pump VSD is reacting to the AHU's call for more cooling. Check the chiller controls that maintain the proper leaving-water temperature as described in:
- Problem: Second chiller is locked out via the DDC system.
- Problem: Failed flow switch prevents second chiller from starting.
- Problem: Chiller fails to start because a failed or closed valve prevents the water-flow switch from making contact.
- Problem: Pump had failed.
- Problem: Flow is imbalanced.
Inspection Step 3
Inspect the direct-digital-control (DDC) system to see if the pressure differential location and setpoint match the original design. Vary the pump speed either through the DDC system or locally at the VSD to see if the pressure reading varies. If it does not, you will need to locally inspect the sensor for proper installation and operation. The sensor may need to be repaired or replaced.
Inspection Step 4
Make sure the cooling-coil valves are operating properly and closing as expected for each AHU. If the system was originally a constant-flow design with 3-way valves, make sure the valve operators were tested or replaced so that they shut off completely when the differential pressure in the system increases.
Inspection Step 5
If the pump speed does not vary at all, make sure there is no short circuit in the piping system that allows supply water to enter the return-water piping without passing through an AHU coil. The first place to look is usually the last place the system was repaired or renovated. Sometimes bypasses are installed at AHUs to allow the system to be flushed out, or the system pressure to be tested.
Inspection Step 6
Make sure the VSD controller is operating in automatic mode and not in local manual or bypass mode. If the controller is in bypass or manual mode, find out why before you return it to automatic operation.
Inspection Step 7
Inspect the system for partially closed valves or clogged strainers. The pump may be trying to overcome a large pressure loss due to some obstruction.
How to Confirm the Problem(s) by Trend Logging
Trend log the following:
- Outside-air temperature (OSAT)
- Pump speed
- Chilled-water supply temperature (CHWST)
- Chilled-water return temperature (CHWRT)
- Differential pressure across the supply and return piping
Normal Operation
The graph below shows normal pump operation varying with system load. The load depends on OSAT, so the pump speed increases as the AHU(s) call for more cooling. The differential temperature of the chilled water increases due to the chilled-water reset schedule. If your graph looks similar to this, the problem should be solved.
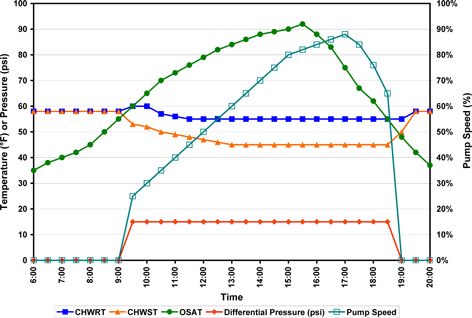
Normal Pump Operation
Abnormal Operation - Constant Pump Speed
The graph below shows the pump speed constant at 80%. The differential pressure between supply and return varies greatly. If your graph looks like this, the automatic controls on your VSD may have been overridden, either by the DDC or locally at the unit. The differential pressure drops as AHUs call for more cooling by opening their control valves. Re-inspect the system starting from Inspection Step 2.
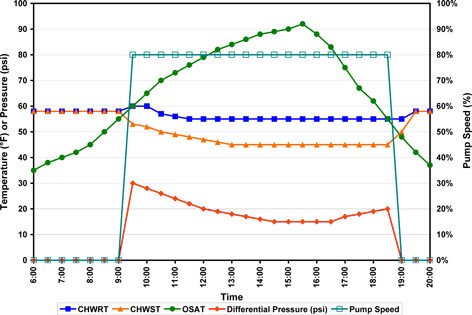
Pump VSD Controls Overridden at 80%
Abnormal Operation - Low Differential Pressure
The graph below shows the pump speed constant at 100%. The differential pressure between supply and return is below the setpoint of 15 psi. If your graph looks like this, you may have a short circuit somewhere in the system, most likely well before the controller location in the piping. The return-water temperature may have dropped due to the short circuit, allowing the chiller to produce only a 5-degree differential.
Also, a clogged strainer or partially closed valve in the chilled-water plant could be creating a high pressure drop. If severe enough, it will also cause the chiller to trip offline due to low flow, and could appear as described in:
Chiller starts and stops frequently:
- Explanation: Load is below the minimum chiller capacity.
- Problem: The chiller is stopped due to a lack of condenser water flow, which triggers the high-pressure-limit switch for the refrigerant.
- Problem: The chiller is stopped due to the high temperature of water entering the condenser, which triggers the high-pressure-limit switch for the refrigerant.
- Problem: Deadband for CHWST (chilled-water supply temperature) is too narrow.
- Problem: The sensor for leaving-water temperature or differential pressure across the evaporator or condenser has failed.
- Problem: Chilled/condenser water pump is cycling. Chiller cycles via the system flow switch.
- Problem: Refrigerant is short.
- Problem: Compressor draws too much current due to wear and tear.
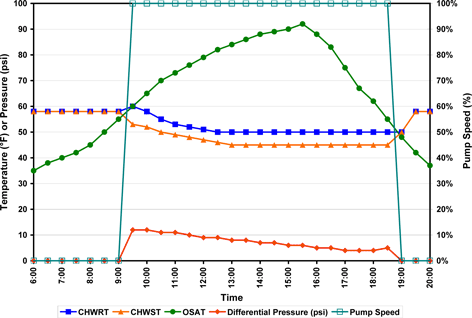
Pump VSD Controls Overridden - System Short Circuit
Labor Skills Required to Find and Resolve the Problem
- DDC system operator/programmer
- Service mechanic